… zur Steigerung der Druckqualität insbesondere bei ABS – zum Nachbauen sicherlich geeignet!
Achtung: Beitrag noch in weiterer Verbesserung!!
Ansich druckt der RF1000 ganz wunderbar mittlerweile – sei es PLA, „Kunst“-Holz Filamente wie Laywood o.ä. oder auch flexible Filamente, bisher gab es kaum was was ich nicht hinbekommen habe. Nur ABS will nicht so richtig und hat eigentlich immer Probleme gemacht mit Verzug, Warping usw. Grund genug an dieser Stelle den Drucker durch eine Einhausung zu verbessern! Die Entscheidung ist auf eine Plexiglas- Aluprofilkombination gefallen – die Materialien sind leicht handzuhaben und ganz bequem in passendem Zuschnitt direkt aus dem Netz zu bestellen.
Folgend die Einkaufsliste:
Plexiglas kam von expresszuschnitt.de, alles in 2 mm Acrylglas XT transparent
2x 532x446mm
1x 362x112mm
1x 362x442mm
1x 362x118mm
1x 362x292mm
1x 362x230mm
1x 350x430mm
Alles für ca. 70 € inkl. MwSt. und innerhalb 1 Woche geliefert und wirklich auf den mm genau zugeschnitten.
Aluminumprofile kamen von aluminium-online-shop.de, alle Winkel 15 x 15 x 2mm AlMgSi0,5
Um Zuschnittkosten zu sparen habe ich 5 Stück x 1m davon bestellt und sie dann später selbst zugeschnitten.
Kosten genau 25 € inkl. MwSt.
Desweiteren noch viele M3 Schrauben + Unterlegscheiben und Muttern mit Ausdrehschutz. Alles aus Edelstahl vom Eisenwarenhändler des Vertrauens für 100 Schrauben / Muttern / Beilagscheiben round about 40 € inkl. MwSt.
Alle 3D gedruckten Teile findet ihr hier: http://www.thingiverse.com/thing:830335
Was wird nun daraus? In etwa das hier:

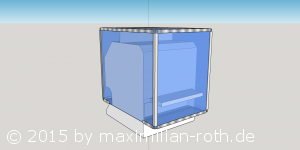
Fangen wir an:
Profile wie folgt zuschneiden:
2x 506mm (obere Abdeckung)
4x 420mm (linke / rechte Seite vorne und hinten)
4x 340mm (unten / oben vorne und hinten)
2x 72,68mm (Überhang vorne links / rechts)
2x 79mm (Überhang hinten links / rechts
Bei den Bohrlöchern will ich keine großen Vorgaben machen: bei allen Profilen, bis auf die ganz Kurzen für den Überhang vorne und hinten, haben wir auf jeder Seite des Profils 3 Löcher gebohrt (je soweit gegeneinander vesetzt, das sich über Eck die Schrauben nicht zu Nahe kommen), bei den kurzen Stücken auf jede Seite eine Bohrung. Wird aus den Bildern später noch ersichtlich – die jetzt kommen 😉
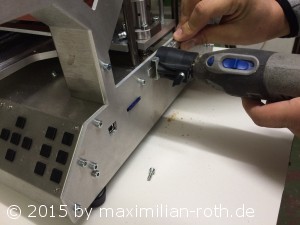
Dieser Schritt war im Nachhinein echt überflüssig und hat unötig viele neue Macken in den Seitenteilen hinterlassen: wir waren der Meinung die leicht herausschauenden Enden der tragenden Elemente beizufräsen damit die Seiten völlig plan sind.
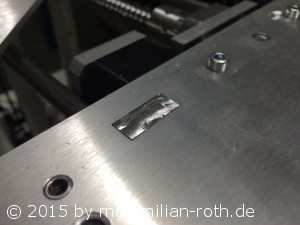
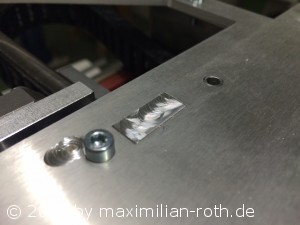
aber egal 🙂
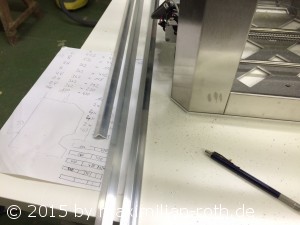
Die zugeschnittenen Profile (noch ohne Löcher)
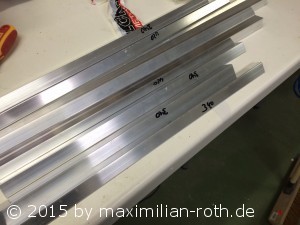
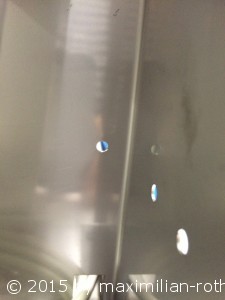
Die einzigen 2 neuen Löcher die in den RF1000 gebort werden müssen befinden sich auf der Rückseite XX cm von den Metalblenden entfernt.
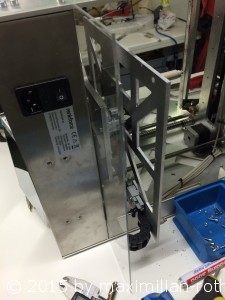
Die Plexiglasplatte hinten muss entsprechend nachbearbeitet werden, dass sie zwischen die beiden Blenden passt, also seitlich soviel weg wie diese Breit sind.
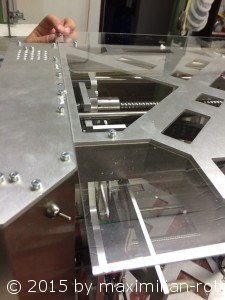
Die seitlichen Plexiglasteile werden auf den flachgelegten Drucker gelegt und die Löcher
von den seitlichen Halteschrauben (Schrauben müssen dafür entfernt werden) abgenommen. Wenn man sich die Bilder genau ansieht bemerkt man, dass wir die Schrauben die die Trägerplatte mit dem Rahmen verbinden ausgespart haben, indem wir einfach die Löcher im Plexiglas so groß ausgebort haben, dass die Schraubenköpfe durchpassen – so kann man diese Schrauben später noch nachjustieren. Die restlichen Löcher (rundherum) werden mit einem M3 Bohrer gebohrt.
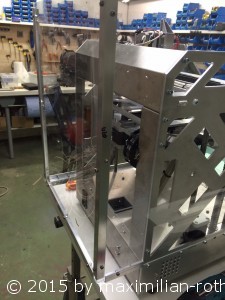
Erste Seite ist dran – Profil wurde angehalten und direkt an den passenden Stellen gebohrt. Für Mutter / Schraube und Unterlegscheibe haben wir immer folgende Reihenfolge genommen:
Innenseite – Mutter | Unterlegscheibe | Alu-Profil | Plexiglas | M3 Schraube – Aussenseite
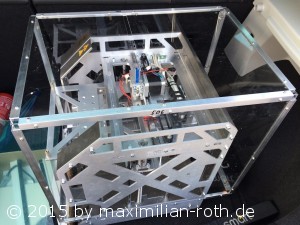
Und da wars schon fertig – sorry, aber ich bin kein großer Verfasser für Bauanleitungen wie ich gerade mal wieder feststellen muss ^^
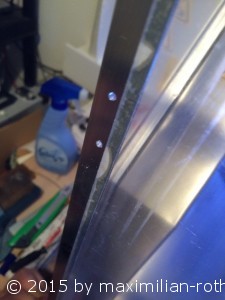
Irgendwas fehlt aber noch… ja die Tür 🙂 Wie im Bild zu sehen ist wurde ein M3 Gewinde ins vordere Profil geschnitten – genau an den beiden Stellen wo man sich ein Scharnier vorstellen könnte.
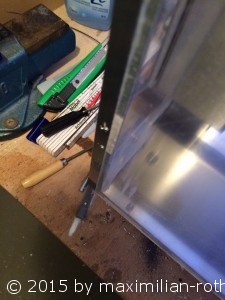
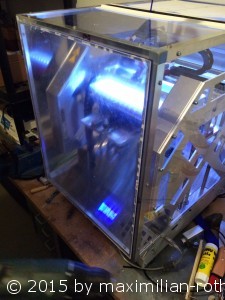
Die vordere Plexiglasplatte wird von Magnetfolie gehalten, die auf dem Türglas selbst und den vorderen Profilen geklebt wurde (mit doppelseitigem Klebeband)
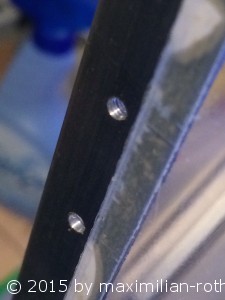
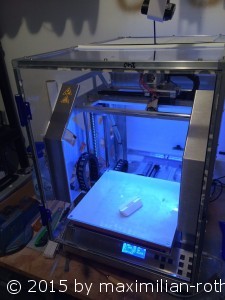
Die Scharniere wurden gerade frisch gedruckt und gleich angebaut!
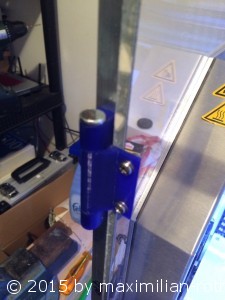
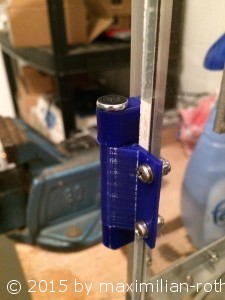
Und ein mehr oder weniger hübscher Knauf mit einem „R“(enkforce)…
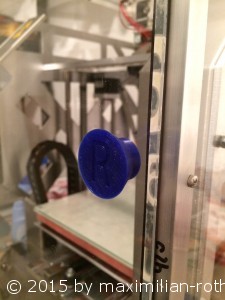
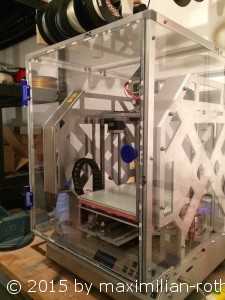
Da steht er nun in seiner vollen (sperrigen) Pracht – man kan ihn gerade noch so alleine Tragen (mindest Armlänge von 63 cm vorrausgesetzt :-))
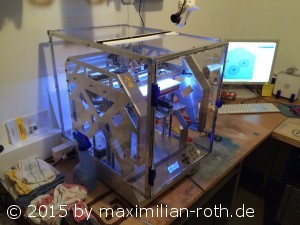
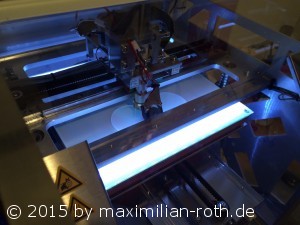
Die Plexiglasplatten sind fast „unsichtbar“
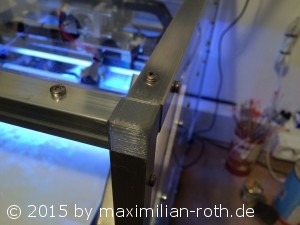
Die wunderschönen Anti-Stoß-Ecken kamen natürlich auch aus dem Drucker.
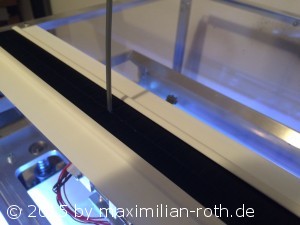
Der „Besen“ ist eine Winddichtung die man sonst unter die Wohnungstür baut (zu finden im gut sortieren Baumarkt).
Der Besen in Aktion:
Alle 3D gedruckten Teile findet ihr hier: http://www.thingiverse.com/thing:830335
So, das wars auch schon – der Beitrag war jetzt etwas schnell dahin „gedängelt“ und wird noch verfeinert. Für Anmerkungen gerne einen Kommentar hinterlassen und nochmals sorry für meine Oberflächlichkeit aber es mangelt bei mir an Motivation ein detailierte Anleitung zu verfassen. Die Sketchupzeichnung die man auf Thingiverse findet (Einhausung_neu.skp) ist maßgetreu und kann als Basis genommen werden.
Ein großer Dank geht hier auch nochmal an meinen Freund Christian auf dessen Konto die ganze Idee und auch der größte Teil der Umsetzung geht! Preiset ihn und seinen riesigen Hobbykeller mit emmens viel Werkzeug und Gerätschaften. Wenn ich mal groß bin will ich auch so einen Hobbyraum 😛
Gute Nacht!
VN:F [1.9.22_1171]
Rating: 4.6/5 (5 votes cast)