Mehr Sein als Schein 😉
Ein guter Freund kam mit einem Projekt um die Ecke, welches zumindest für mich nicht alltäglich erschien. Es ging darum einen Raspberry Pi gekonnt in ein Commodore C64 Gehäuse einzubauen um diesen später mit dem RetroPie System zu bespielen und in eine Multifunktions-Emulations Spielekonsole zu verwandeln.
Ohne den 3D Drucker wäre das ganze Unterfangen komplizierter geworden, so wurde es zwar nicht zu einem Kinderspiel aber dennoch zu einem anspruchsvollen Werk, was Maßgenauigkeit anbetraf.
Offcamera wurde erstmal obligatorisch die entsprechenden Öffnungen und Schraubenaufnahmen im Gehäuse vermessen und die Daten in Sketchup übernommen, in dem die einzelnen Teile entstanden sind:
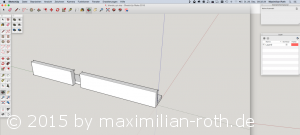
Ein erster Test: die 2 großen Öffnungen auf der Rückseite des C64 ausfüllen für die spätere Steckerkonsole
(vom ersten Einpassen habe ich leider kein Bild gemacht)
Ok, ran an den Slicer und ab zur Plastik-Schmelzmaschine…
Die gibts hier zu kaufen
Finale – alle Kabel verlegt und gebunden. Gehäuse kann geschlossen werden.
Ein paar kleine Details:
- am Raspberry Pi wurde eine Stiftleiste an den 2 unbestückten Pins für den Powertaster eingelötet und dort der rote Taster auf der Rückseite des Gehäuses angeschlossen
- Da wir ein gerregeltes 5 Volt Netzteil verwendet haben wurde die DC Buchse direkt mit den Pins auf der GPIO Leiste des Raspberry Pi verbunden
- Wir haben direkt eine USB Leitung an die Keyrah Platine gelötet
Was bleibt noch zu sagen? Alle Teile passten so ziemlich auf Anhieb ohne große Nachbearbeitung mit Feile und Schmiergelpapier, wie es sonst schon oft der Fall war. Es steht und fällt sehr viel mit der Komplexität der Teile und der Möglichkeit im Vorfeld alles genau auszumessen. Da das gut von der Hand ging, war auch das genaue Erstellen der Teile nicht so schwer.
Anbei noch ein paar weitere Impressionen:
Alles restlichen Bauteile wie USB Buchsen usw. wurden bei Pollin Elektronik gefunden.
Das Projekt ist hier zu finden. Über Nachbauten würde ich mich freuen (und gerne auch über Feedback!!)
Vielen Dank an Sebastian Scholten, dessen Idee die Sache hier war.
Nachtrag (17.07.2016):
Für die USB „Buchsen-Halteklammer“ habe ich M3 Schrauben verwendet, ca. 1 cm lang (mit Senkkopf). Die anderen Schrauben sind aus meinem „PC-Schrauben Fundus“, sollten aber glaub ich auch M3 gewesen sein, die sehr schön in die Montageaufnahmen im C64 Boden passten.
Nachtrag:
Ich freue mich immer wenn es Leute gibt, die Spaß an ähnlichen Dingen haben und auch mal etwas nachbauen, was hier zum Besten gegegeben wird: https://steffenweise.wordpress.com/2016/07/31/c314-neuer-wein-in-alten-schlaeuchen/